Intern Insight: Turbine Testing at Alden Labs
During the last half of 2019, the Emrgy engineering team conducted product testing of our next generation twin-turbine module in partnership with Alden Research Laboratory. As an engineering intern, I got the opportunity to travel to the testing facility in Holden, Massachusetts and assist with data collection. The Turbine Test Facility at Alden consisted of a wide recirculating flume about 80 feet long with two large thrusters to pump water through the test section. This setup was used to simulate a wide range of flow conditions in order to better understand the module’s performance across its entire operational envelope and also to compare the performance of different turbine configurations in varying conditions.
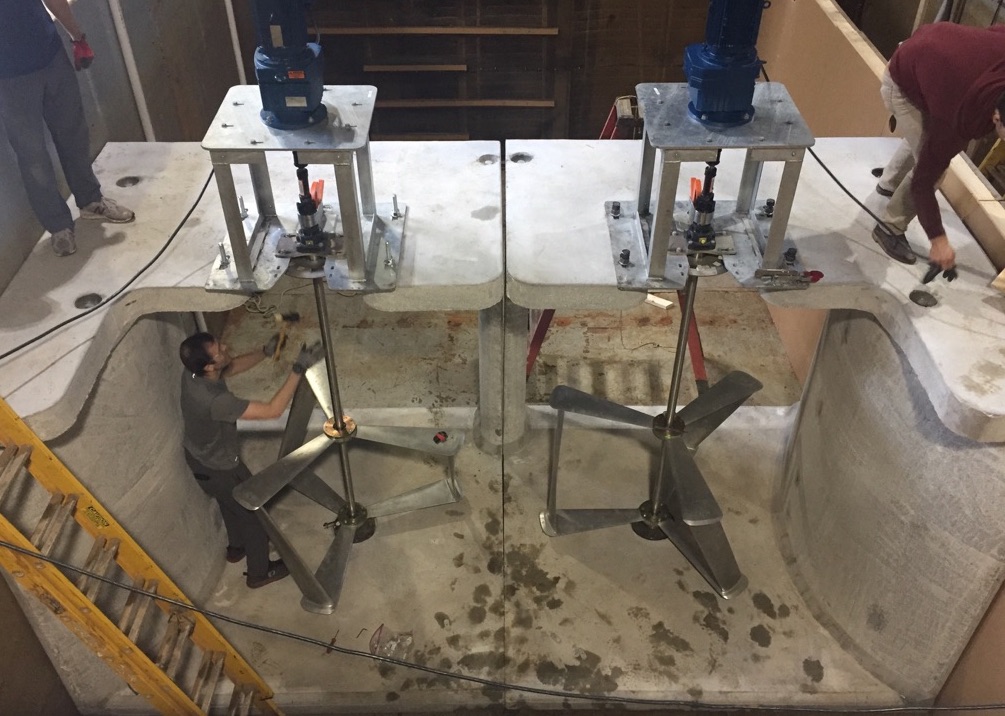
The engineering team finishes assembling the turbine system and preps for testing.
At the start of a typical day of testing, we would check to make sure the system was ready to go, begin filling the empty flume with water (which could take over an hour because of the massive volume of the testing setup), and then turn on the thrusters to get the water flowing. After this, we could start up the turbines and begin running tests. Usually, this would involve monitoring quantities of interest (like power output of the system, torque on the shaft coupling, or water level change) as we change other testing parameters (such as the flow conditions, the speed of the rotor, or the type of rotor). Changing turbine configurations was especially tricky because the flume had to be drained in order to remove the previous blades and spokes and install the new ones. On a given day, we would run anywhere from 10 to 40 different tests, and overall, we tested 14 unique turbine system configurations!
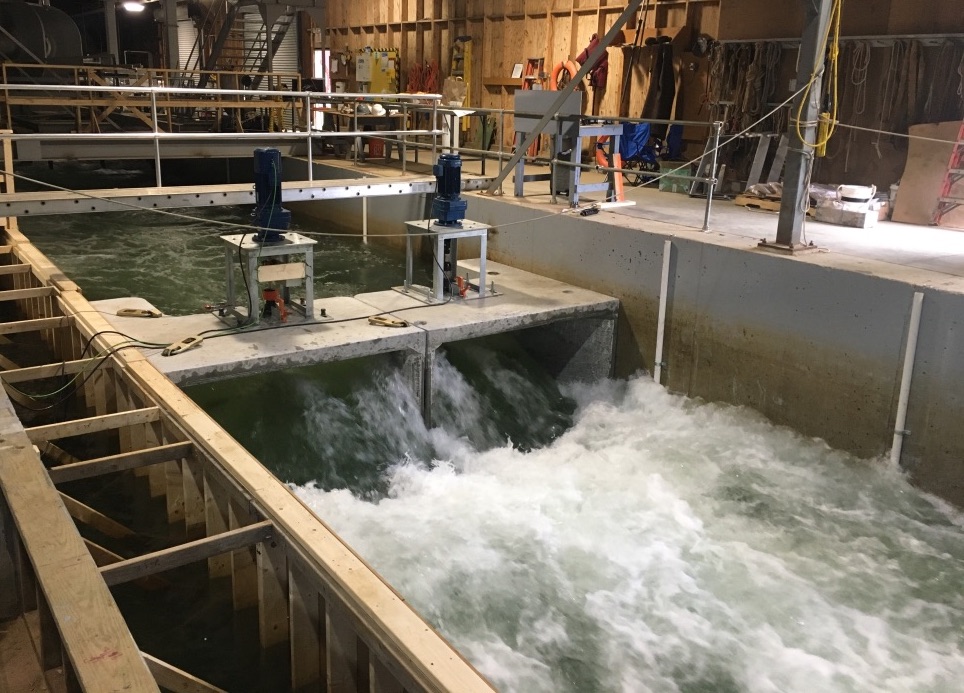
Product testing commences as we flow up to 450 cubic feet of water per second through the turbine module.
This experience gave me the opportunity to apply experimental procedures I learned in my classes and to see how large-scale product testing is conducted in the real world. Earlier on in my internship, I had designed a tool for inserting and removing tight-fitting dowel pins from the turbine hub in order to speed up the process of switching between turbine configurations. The most exciting part of the trip for me was using the tool I designed to assemble and disassemble the turbines during testing. The tool allowed us to go from manually hammering dowel pins into place to quickly inserting and removing them using an impact drill and it cut down turbine assembly time by almost 50%.
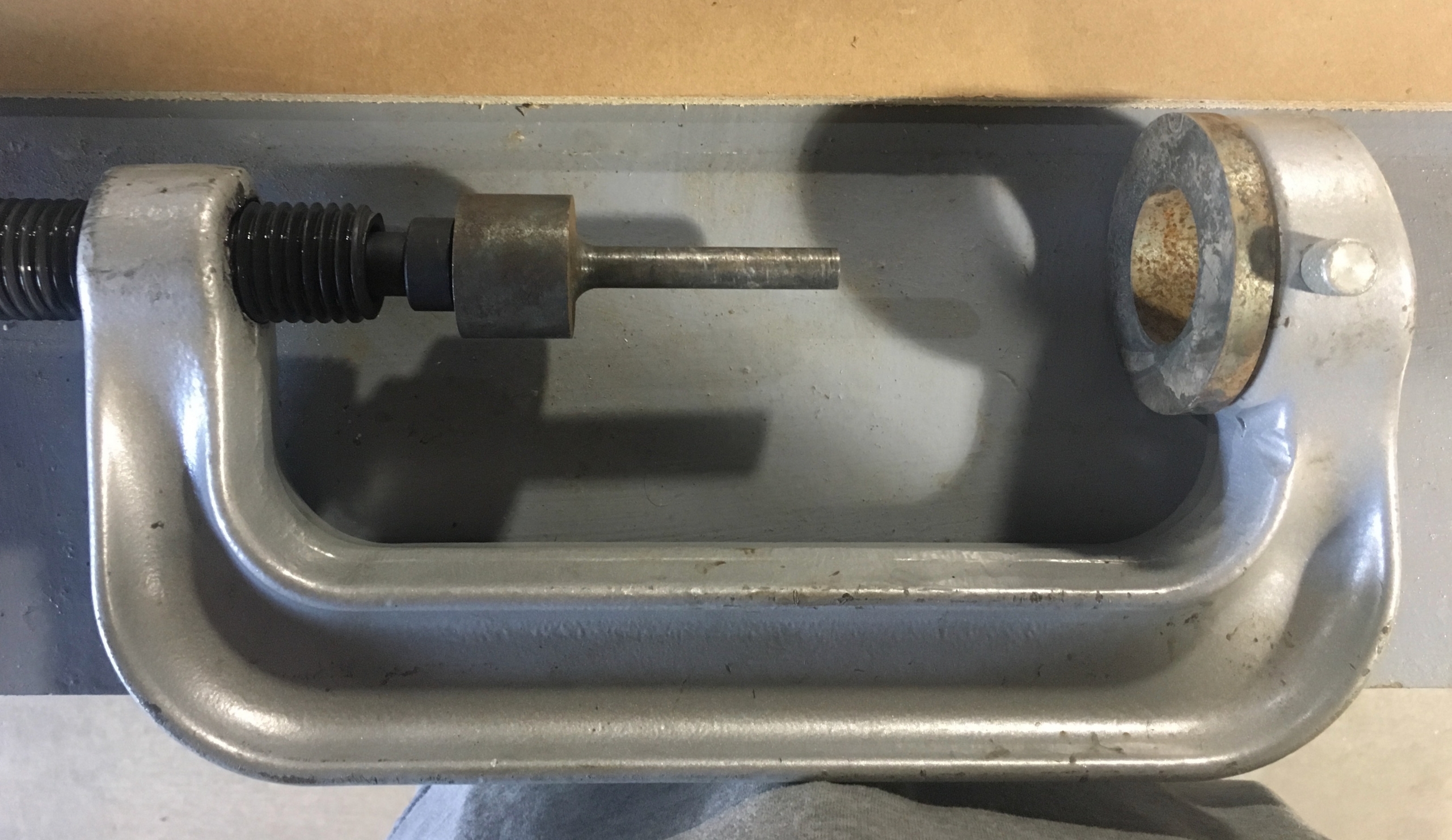
Attached to this large C-frame and forcing screw are two of the components I designed for removing dowel pins.
The product testing we conducted at Alden allowed us to collect data that will inform future design decisions and enable us to more accurately predict our system performance based on a customer’s site conditions. For me, this was an invaluable experience from which I gained important engineering know-how and got the chance to be a part of a pivotal company project.